Elkom: Your Guide to Vacuum Membranes and Systems
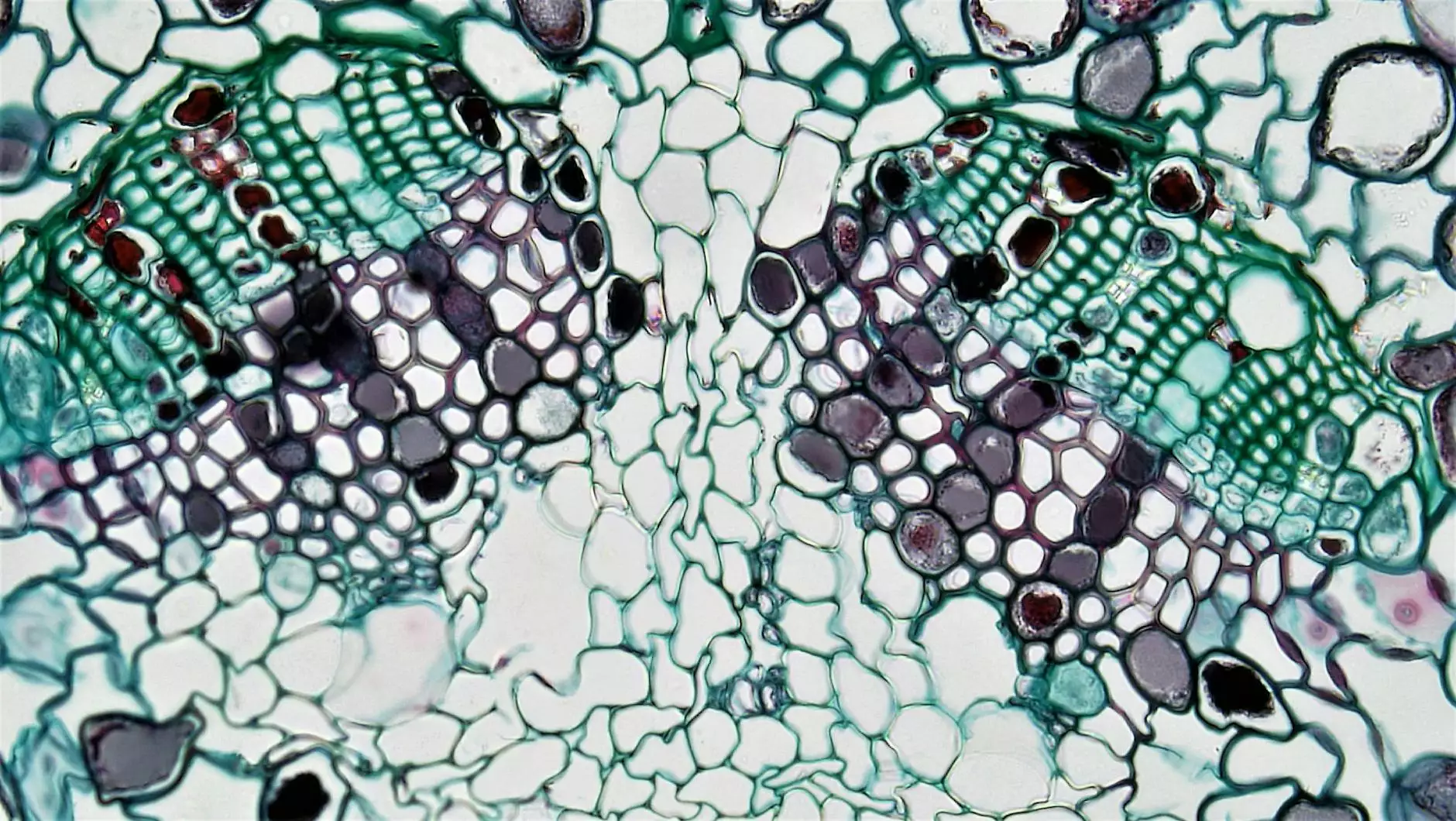
Elkom is more than just a term; it embodies a welcoming approach to understanding vacuum technology, membranes, and systems. In this comprehensive guide, we will delve deep into various types of membranes such as silicone membranes, rubber membranes, and essential vacuum system parts. Whether you are a manufacturer, designer, or simply someone interested in vacuum technology, this article will provide you with the knowledge you need.
Understanding Vacuum Membranes
Vacuum membranes are crucial components in many industrial applications. They create a barrier that ensures optimal functioning of equipment by maintaining the integrity of the vacuum environment. Let's explore the various types of membranes available and their uses.
1. Silicone Membranes
Silicone membranes are widely recognized for their excellent flexibility and durability. They are resistant to extreme temperatures and can withstand a significant amount of wear and tear. Here are some key benefits of silicone membranes:
- High Temperature Resistance: They can operate efficiently in both high and low-temperature environments.
- Chemical Resistance: Silicone materials are non-reactive, making them ideal for various chemical applications.
- Durability: Silicone membranes have a long lifespan, reducing the need for frequent replacements.
2. Rubber Membranes
When we refer to rubber membranes, we are talking about incredibly versatile materials suitable for a range of applications. Rubber membranes are often used in conjunction with various vacuum systems. Here are some advantages of rubber membranes:
- Flexibility: They provide excellent flexibility and can be tailored to fit different applications.
- Cost-Effectiveness: Rubber membranes tend to be more economical compared to other materials, making them a popular choice among manufacturers.
- Sealing Properties: They create effective seals, essential for maintaining the necessary vacuum pressure within systems.
Essential Vacuum System Parts
To achieve efficient functionality, understanding the various vacuum system parts is crucial. Here’s a closer look at the components that make up a reliable vacuum system:
1. Vacuum Pumps
Vacuum pumps are the heart of any vacuum system. They create the necessary vacuum pressure by removing air and other gases from the chamber. Different types of vacuum pumps are available, including:
- Rotary Vane Pumps: Recognized for their reliability and efficiency, ideal for a range of applications.
- Diaphragm Pumps: Perfect for applications requiring chemical resistance, providing consistent vacuum levels.
- Scroll Pumps: Known for their quiet operation, making them suitable for laboratory environments.
2. Vacuum Chambers
The vacuum chamber is the space where the vacuum is created and maintained. These chambers come in various sizes and materials, depending on the application requirements. Factors to consider when selecting a vacuum chamber include:
- Material Compatibility: Ensure the material can withstand the environment and chemicals used.
- Size Requirements: The size must be appropriate for the volume of items being processed.
- Pressure Ratings: Consider the maximum vacuum levels needed for your application.
3. Valves and Fittings
Valves and fittings play a pivotal role in controlling the flow of gases within a vacuum system. Their proper selection ensures the integrity and efficiency of the system:
- On/Off Valves: Used to isolate the vacuum chamber from external influences.
- Check Valves: Prevent backflow, maintaining the vacuum integrity.
- Quick Couplings: Ensure easy connection and disconnection of components for maintenance and operation.
Natural Rubber Membranes
When it comes to innovative materials, natural rubber membranes are gaining traction for their eco-friendliness and durability. Natural rubber offers several advantages:
- Biodegradable: An environmentally-friendly option compared to synthetic alternatives.
- Elasticity: Provides excellent stretch and recovery properties, essential for various vacuum applications.
- Adhesive Properties: Natural rubber membranes have great adhesion, making them ideal for applications that require sealing.
Choosing the Right Membrane and System for Your Needs
Choosing the right vacuum membrane and system requires thorough understanding and considerations:
1. Assess Application Requirements
Before selecting a membrane, assess your operational needs, including:
- Temperature conditions where the membrane will operate.
- Chemical compatibility with materials used in your processes.
- The required lifespan of the membrane under specific conditions.
2. Consult with Experts
Don't hesitate to consult with industry experts, such as those from vacuum-presses.com, who can guide you in making the right choice based on your unique needs.
3. Consider Future Needs
When selecting membranes and components, always consider potential future expansions or changes in your processes. This foresight can save costs and streamline your operations.
The Future of Vacuum Technology
As industries continue to evolve, so does vacuum technology. Innovations in membrane materials, system designs, and applications are on the rise. Here are some trends to watch:
- Advancements in Material Science: Development of new materials that enhance durability while remaining eco-friendly.
- Automation: Integration of automated systems for better control and efficiency in vacuum processes.
- Environmental Considerations: Increasing focus on eco-friendly solutions, influencing product designs and material choices.
Conclusion
Elkom serves as a crucial concept for anyone involved in vacuum technology, whether through understanding the various types of membranes or the intricacies of vacuum systems. By remaining informed about the products available at vacuum-presses.com, you can make educated decisions that enhance your operational efficiency and sustainability.
Navigating the world of vacuum technology may initially seem daunting, but with the right knowledge and resources, you can easily find the solutions that best meet your needs. Always remember, investing in high-quality membranes and system parts is a key to success.