Plastic Injection Molding in China: Quality, Efficiency, and Innovation
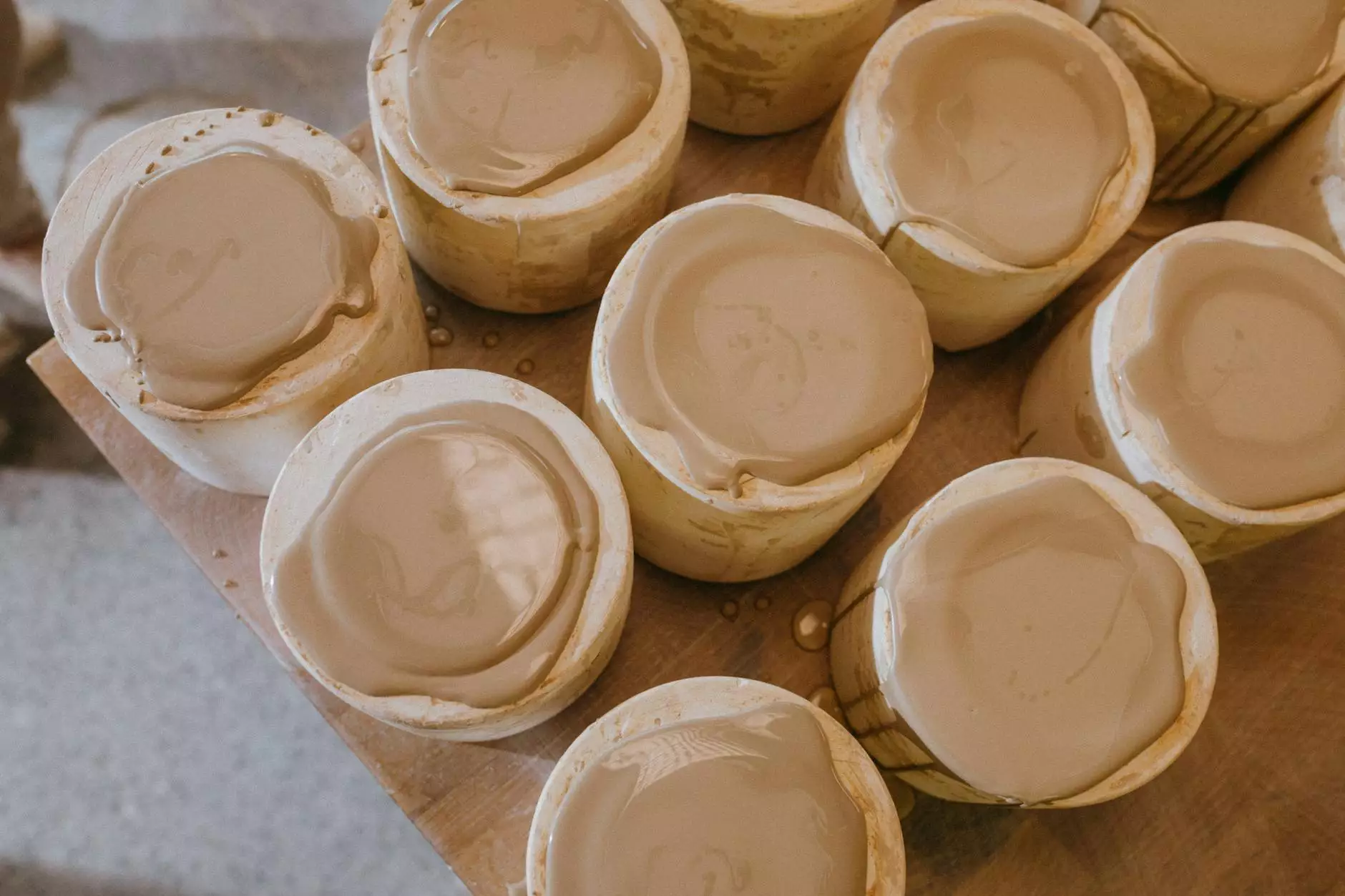
In the ever-evolving landscape of global manufacturing, plastic injection molding in China has emerged as a leader in innovation and efficiency. As companies continuously seek to optimize their production processes while minimizing costs, China has established itself as a powerhouse in the field of plastic injection molding, thanks to its superior technology, skilled labor force, and state-of-the-art facilities.
The Rise of Plastic Injection Molding in China
Plastic injection molding is a manufacturing process for producing parts by injecting molten material into a mold. This method is particularly favored for its capability to produce high volumes of parts with consistent quality and precision. Over the past few decades, China has become the go-to destination for plastic injection molding, largely due to several vital factors:
- Cost-Effectiveness: The lower labor and material costs in China make it economically advantageous for businesses to outsource their manufacturing needs.
- Advanced Technology: Chinese manufacturers are increasingly adopting the latest technologies and equipment, enabling them to produce high-quality plastic components.
- Skilled Workforce: China boasts a large pool of skilled workers trained in advanced manufacturing processes, ensuring high-quality output.
- Rapid Turnaround Time: Manufacturers in China can mobilize quickly, allowing for faster production times and reduced lead times.
Understanding the Process of Plastic Injection Molding
The process of plastic injection molding involves several critical steps that ensure the production of high-quality parts. Understanding these steps is essential for businesses considering partnering with a Chinese manufacturer:
1. Design and Prototyping
The first step in the plastic injection molding process is designing the part. Engineers use advanced CAD software to create 3D models and prototypes. This phase is crucial as it provides insight into how the final product will look and function.
2. Mold Creation
Once the design is finalized, the next step is mold creation. This involves:
- Using CNC machines to craft the mold from steel or aluminum, ensuring every detail of the design is captured.
- Applying surface treatments to enhance durability and improve the finish of the molded parts.
3. Injection and Cooling
The process moves on to injecting the molten plastic into the mold. Key aspects include:
- Temperature Control: Maintaining the right temperature is vital for achieving the desired viscosity of the plastic.
- Cooling Time: Allowing the plastic to cool and solidify properly ensures the dimensional accuracy of the final product.
4. Ejection and Finishing
After cooling, the mold opens, and the solidified part is ejected. Additional finishing processes may include:
- Trimming: Removing any excess material.
- Surface Finishing: Including painting or coating to enhance appearance and protect against wear.
Advantages of Partnering with Chinese Manufacturers
When businesses opt for plastic injection molding in China, they gain access to a multitude of advantages:
1. Competitive Pricing
Due to lower production costs, businesses can save significantly on their manufacturing expenses, making products accessible at more competitive prices. This competitive edge can be a game-changer in saturated markets.
2. High-Quality Standards
Many Chinese manufacturers have obtained international quality certifications, such as ISO 9001. This commitment to quality ensures that products meet stringent global standards, reducing the risk of defects.
3. Customization Capabilities
Chinese manufacturers are known for their flexibility and willingness to accommodate custom designs. This adaptability can be crucial for businesses looking to differentiate themselves in the marketplace.
4. Scalability
With vast production facilities and resources, Chinese manufacturers can easily scale operations up or down based on demand. This scalability allows businesses to respond quickly to market changes.
Factors to Consider When Choosing a Manufacturer
While the benefits are clear, selecting the right Chinese manufacturer for plastic injection molding is critical. Here are some key factors to keep in mind:
1. Experience and Reputation
Research the manufacturer’s track record and reputation in the industry. Look for reviews, case studies, and testimonials from past clients to gauge their reliability and quality.
2. Technology and Equipment
Assess the technology and machinery used by the manufacturer. Advanced facilities that use the latest injection molding technology are more likely to produce high-quality parts.
3. Communication Skills
Effective communication is essential for a successful partnership. Ensure the manufacturer has English-speaking staff and can clearly understand and meet your requirements.
4. Compliance with Industry Standards
Confirm that the manufacturer adheres to local and international safety and quality standards, as these practices will impact the quality of your products.
The Future of Plastic Injection Molding in China
The future of plastic injection molding in China looks promising as the industry continues to evolve. Trends such as increased automation, the use of sustainable materials, and the integration of smart manufacturing processes are shaping the landscape:
1. Automation and Smart Manufacturing
With the rise of Industry 4.0, Chinese manufacturers are integrating automation into the injection molding process. This not only enhances production efficiency but also reduces human error and improves safety.
2. Sustainability Trends
As global awareness of environmental issues grows, manufacturers are investing in sustainable practices. The use of recyclable materials and energy-efficient processes is becoming a priority in the industry.
3. Innovation in Materials
There is ongoing research into new types of plastics and composites that offer better performance and are more sustainable. This innovation will drive future developments in plastic injection molding.
Conclusion
In conclusion, investing in plastic injection molding in China presents an incredible opportunity for businesses aiming to enhance their manufacturing processes. With cost-effective solutions, outstanding quality, and the capacity for customization and scalability, Chinese manufacturers stand out as leaders in the industry. Companies like DeepMould.net exemplify this level of excellence, providing clients with high-quality molded products tailored to their unique specifications. As the industry continues to innovate and adapt, partnering with a Chinese manufacturer for plastic injection molding could very well be the key to unlocking new levels of success for your business.
plastic injection molding china