Understanding Plastic Mould Tooling: A Comprehensive Guide
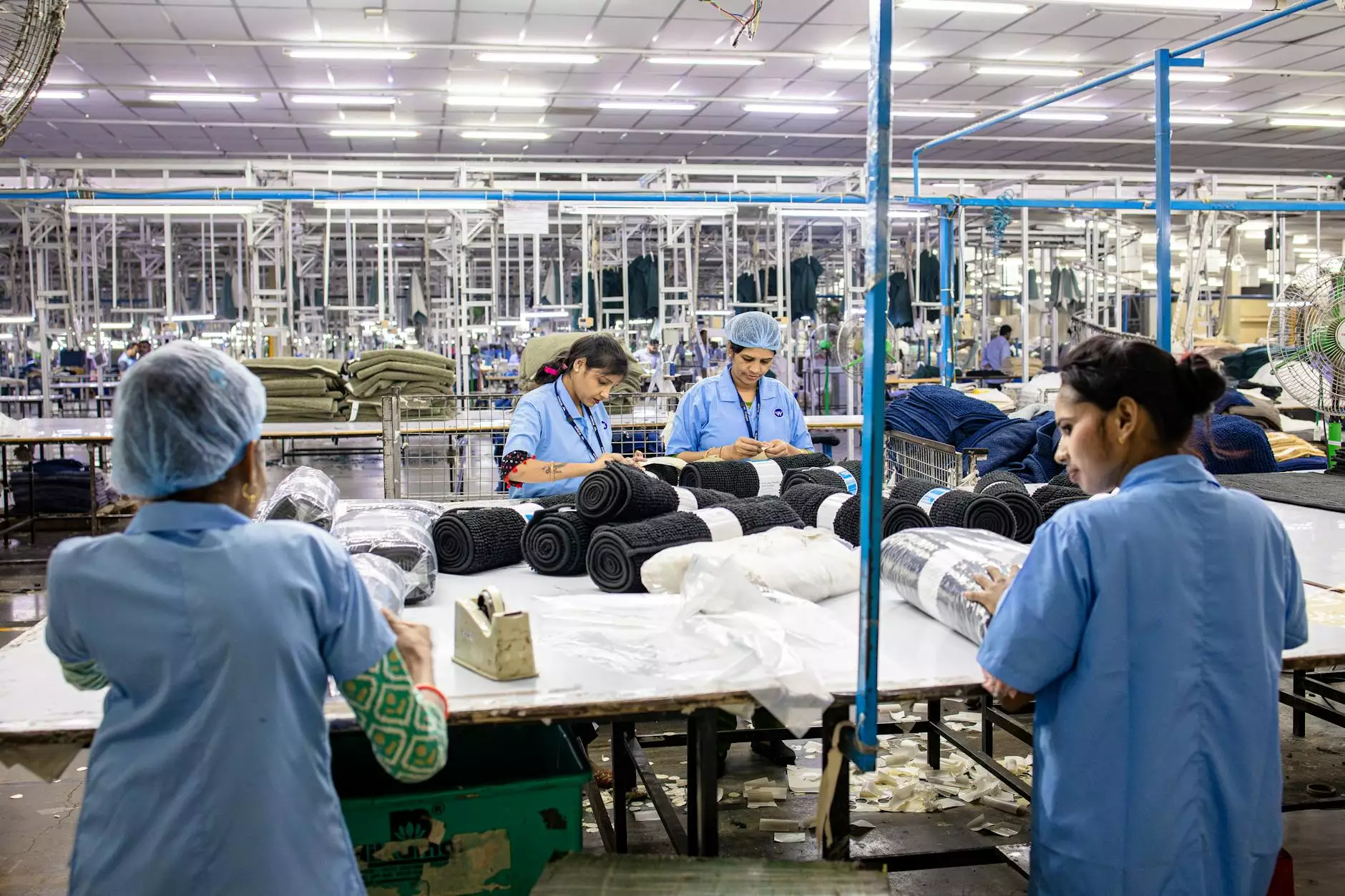
In the realm of modern manufacturing, plastic mould tooling stands as a pivotal process that enhances efficiency, quality, and cost-effectiveness in production. This article delves deep into the intricacies of plastic mould tooling, exploring its significance, applications, and the advantages it offers to metal fabricators. By the end of this guide, readers will gain a comprehensive understanding of the topic and its relevance in today's manufacturing landscape.
What is Plastic Mould Tooling?
Plastic mould tooling refers to the process of creating tools that shape molten plastic into predetermined forms. This technology plays a crucial role in the mass production of plastic components used in various industries such as automotive, consumer goods, electronics, and medical devices.
The Importance of Plastic Mould Tooling
The significance of plastic mould tooling cannot be understated. It is a critical factor that determines the quality, durability, and precision of the final product. Here are several key reasons why plastic mould tooling is essential:
- Cost Efficiency: Effective tooling minimizes material waste and reduces production costs, making it an economical choice for manufacturers.
- High Precision: Well-designed moulds ensure that every piece is manufactured to exact specifications, which is vital for industries that rely on tight tolerances.
- Consistency and Quality: Mould tooling produces consistent products, maintaining quality across large production runs.
- Complex Designs: Modern tooling techniques allow for the creation of intricate designs that would be impossible with traditional methods.
The Process of Creating Plastic Mould Tools
The creation of plastic mould tooling involves several detailed steps, each requiring precision and expertise. Here’s a step-by-step breakdown:
1. Conceptualization and Design
The first step in the tooling process is conceptualizing the mould design. This involves collaboration between engineers and designers to understand the requirements of the part to be produced. Advanced software tools, such as CAD (Computer-Aided Design), are often utilized to create detailed 3D models of the mould.
2. Material Selection
The choice of material for the mould is integral to the process. Materials such as steel and aluminum are commonly used due to their durability and ability to withstand high temperatures. The specific application and volume of production will often dictate the material choice.
3. Machining the Mould
At this stage, the actual mould is machined from the selected material. Using CNC (Computer Numerical Control) machines allows for high precision in shaping the mould according to the design specifications. This phase is crucial as any errors can result in costly reworks.
4. Testing and Refinement
Once the mould is created, it undergoes rigorous testing. This stage identifies any flaws or adjustments needed for ensuring optimal functionality. It may involve running prototype cycles to see how the mould performs in practice.
5. Production Launch
After comprehensive testing and refinement, the mould is ready for production. This stage involves integrating the moulding process into the production line, utilizing machinery to produce the plastic components on a large scale.
Applications of Plastic Mould Tooling
Plastic mould tooling finds applications across diverse sectors, making it an indispensable tool in manufacturing. Here are some notable applications:
1. Automotive Industry
In the automotive sector, plastic parts are crucial for various components, from dashboards to exterior trims. Tooling enables the efficient production of lightweight yet durable parts that meet stringent safety and performance standards.
2. Electronics Manufacturing
The electronics industry heavily relies on plastic moulding for items such as casing for phones, laptops, and connectors. Precision is critical here, as small deviations can affect the functioning of electronic devices.
3. Medical Devices
In the medical field, the production of disposables and advanced devices often utilizes plastic mould tooling. Tools must meet strict regulatory standards and ensure hygienic manufacturing processes.
4. Consumer Goods
Everyday consumer products, including packaging, toys, and household items, are produced using plastic mould tooling. This versatility enables manufacturers to cater to evolving consumer preferences and market demands.
Advantages of Using Plastic Mould Tooling
The advantages of adopting plastic mould tooling in manufacturing processes are profound:
- Increased Production Speed: Once a mould is created, production can occur at a rapid pace, accommodating large volumes in shorter timeframes.
- Enhanced Product Lifespan: High-quality moulds often result in products that are more robust and have longer lifespans, reinforcing brand reputation.
- Flexibility: Moulds can be modified or replaced easily, allowing businesses to adapt to new trends and requirements without significant investments.
- Environmental Benefits: Efficient moulding processes lead to reduced material waste, aligning with sustainability goals and environmental regulations.
The Future of Plastic Mould Tooling
As we advance further into the 21st century, the future of plastic mould tooling looks promising. Innovations in technology, particularly in automation and 3D printing, are set to revolutionize the moulding industry. Here are potential changes we may witness:
1. Automation and Robotics
The integration of automation in the moulding process is likely to increase efficiency and reduce human error. Robotics can take over repetitive tasks, allowing skilled workers to focus on complex problem-solving and innovation.
2. 3D Printing in Tooling
3D printing technology is making strides in the production of moulds, offering rapid prototyping and the ability to create complex geometries that traditional methods may struggle with. This will potentially lower costs and increase the agility of production operations.
3. Sustainable Practices
With the growing emphasis on sustainability, manufacturers are expected to adopt greener practices in their tooling processes. This could include the use of recyclable materials or energy-efficient machinery, aligning production methods with global environmental goals.
Conclusion
In conclusion, plastic mould tooling is a cornerstone of modern manufacturing that serves multiple industries. Its importance in enhancing productivity, improving quality, and driving innovation cannot be overlooked. For businesses in the metal fabrication sector, understanding and leveraging this technology will be key to staying competitive in an ever-evolving market. If you’re looking to explore expert insights and services regarding plastic mould tooling, visit DeepMould.net today for more information.