Understanding the **Low Pressure Casting Process**
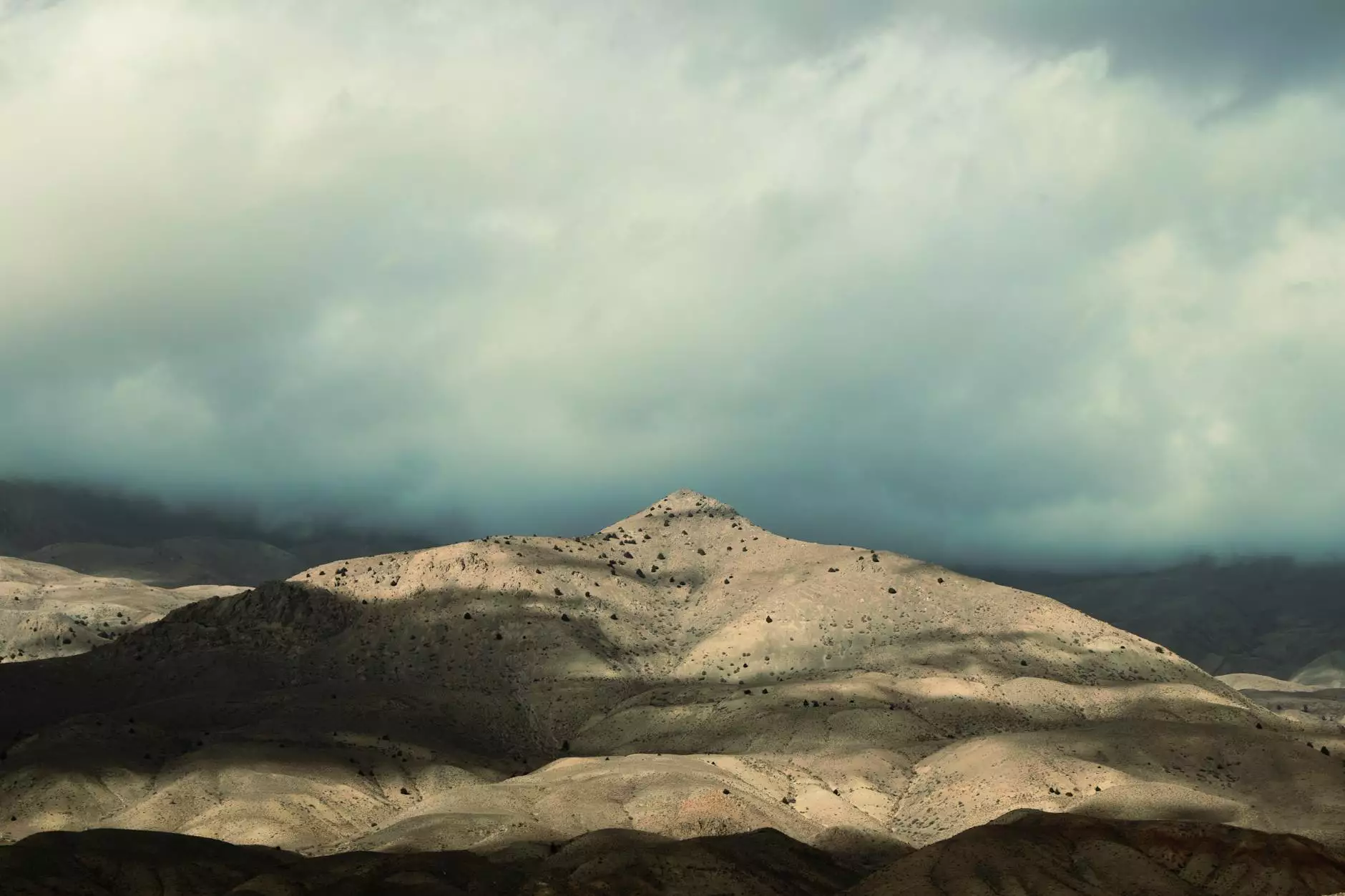
The low pressure casting process is an innovative method primarily used in the manufacturing of metal components, particularly in industries that demand high precision and efficiency. This process is gaining traction in various sectors, including Art Supplies, Product Design, and 3D Printing. In this in-depth guide, we will explore the intricacies of the low pressure casting process, its benefits, applications, and how it compares to other casting methods.
What is the Low Pressure Casting Process?
The low pressure casting process involves pouring molten metal into a mold through a controlled low-pressure system. Unlike traditional gravity casting, where the metal flows freely into the mold under the influence of gravity, low pressure casting employs a sophisticated system to ensure optimized flow and filling of the mold cavity.
How Does Low Pressure Casting Work?
During the low pressure casting process, several key steps are followed:
- Mold Preparation: The first step involves creating a high-quality mold, typically made from materials like sand or metal. This mold is designed to withstand the pressure applied during the casting process.
- Filling System Assembly: A filling system is integrated with the mold, allowing molten metal to be directed into it. The system is crucial for controlling the pressure and flow rate of the metal.
- Molten Metal Heating: The metal is heated until it reaches a liquid state. Common metals used in this process include aluminum and magnesium alloys due to their favorable properties.
- Pressurized Casting: The molten metal is introduced into the mold at low pressure, typically ranging from 0.5 to 2 bars. This controlled pressure helps in achieving complete filling and minimizes the occurrence of air bubbles.
- Curing and Cooling: Once the mold is filled, the metal is allowed to cool and solidify. After cooling, the mold is removed, and the final product is retrieved.
Benefits of the Low Pressure Casting Process
The low pressure casting process offers numerous advantages over traditional casting methods:
- Precision: It produces components with superior dimensional accuracy and surface finish, making it ideal for intricate designs.
- Reduced Defects: The low pressure minimizes turbulence, leading to fewer defects such as air pockets and inclusions.
- Material Efficiency: The process allows for better material usage, with less waste compared to other casting techniques.
- Cost-Effectiveness: With advancements in technology, the low pressure casting process can be highly economical, particularly for medium to large production runs.
- Versatility: It is suitable for a wide range of materials, making it a flexible option for various applications.
Applications in Various Industries
The low pressure casting process finds applications across multiple industries, due to its ability to produce high-quality components. Some notable areas include:
1. Art Supplies
In the realm of art supplies, manufacturers leverage low pressure casting to create intricate molds and sculptures. This technique allows artists to replicate detailed designs with outstanding accuracy while using a variety of metals, enhancing the durability and aesthetic appeal of their crafts.
2. Product Design
Low pressure casting plays a crucial role in product design. Designers benefit from the ability to prototype quickly with high fidelity. The process enables them to test designs and iterate on products efficiently, leading to faster times to market without compromising quality.
3. 3D Printing
In the field of 3D printing, low pressure casting can be used to create molds for printing complex geometries. By producing metal molds, manufacturers can achieve a higher level of detail and functionality in their printed products, thereby elevating the entire 3D printing process.
Comparing Low Pressure Casting to Other Casting Methods
While the low pressure casting process has specific advantages, it's essential to understand how it stacks up against other techniques.
1. Gravity Die Casting
Gravity die casting relies on gravitational forces, which can lead to challenges in filling complex molds. In contrast, low pressure casting provides controlled flow, significantly reducing defects.
2. High Pressure Die Casting
High pressure die casting involves injecting molten metal into a mold under high pressure, which can lead to increased production speed. However, it is often not as precise as the low pressure method and may result in more waste material.
3. Sand Casting
Sand casting is a traditional method known for its versatility and low cost. However, it typically lacks the precision and surface finish provided by low pressure casting, making it less suitable for intricate designs.
Considerations When Choosing the Low Pressure Casting Process
When considering the low pressure casting process, several factors should be evaluated:
- Material Selection: Understand which materials can be effectively utilized in the low pressure casting process. Common choices include aluminum and magnesium, but the specific application may dictate others.
- Mold Design: Ensure that the mold design accommodates the characteristics of low pressure casting, promoting optimal metal flow and cooling.
- Production Volume: Assess whether your production volume justifies the investment in low pressure casting technology.
- Quality Requirements: Define the required tolerances and surface finishes for your project to determine if low pressure casting can meet these standards.
Future of Low Pressure Casting in Manufacturing
The future of the low pressure casting process looks promising as industries continue to seek more efficient and cost-effective manufacturing methods. As technological advancements emerge, we can anticipate improvements in:
- Automation: Enhanced automation systems will likely streamline the casting process, reducing labor costs and improving consistency.
- Materials Science: Ongoing research into new alloys and materials can expand the applications of low pressure casting.
- Integration with Digital Technologies: The convergence of casting and digital technologies, such as simulation software, will lead to better mold designs and faster production times.
Conclusion
The low pressure casting process is a sophisticated and efficient technique that has transformed the manufacturing landscape in various sectors, including Art Supplies, Product Design, and 3D Printing. Its precision, reduced defects, and cost-effectiveness make it a preferred choice for many applications.
As industries evolve and demands for quality and efficiency increase, understanding the nuances of the low pressure casting process becomes crucial for manufacturers and designers. By embracing this innovative method, businesses can elevate their product offerings and remain competitive in a rapidly changing market.
For more information and insights into the low pressure casting process, visit us at Arti90.com.